- Home
- Technical Products
Enterprise Cloud IT Solutions
Test Measurement
Industrial Measurement
- Solutions
Enterprise Cloud IT Solutions
Test Measurement
- Resource Center
- About Us
EN
Hongke Articles
CAN+BMS: How can HONGKE CAN card "renew" the power of new energy battery?
Battery Management System (BMS) in Chinese is a power battery management system. Battery management system for electric vehicles, that is, the battery monitoring and management system, this technology enables the car to meet the high-performance requirements of various programs play a role, through the voltage, current, temperature, and SOC parameters such as acquisition, calculation, and further control of the battery charging and discharging process, to achieve the protection of the battery. Real-time monitoring and control of the battery pack is essential in electric vehicles to enhance the overall performance of the battery management system, which is an important link between the on-board power battery and the electric vehicle, which is exactly the CAN communication, and that is where our PCAN comes in.
I. What can BMS do?
Through CAN communication, the BMS can provide accurate, up-to-date information about the status of the battery pack, including its temperature, voltage and other key parameters that are critical to ensuring the safe and efficient operation of the battery pack.
As long as a notebook and a CAN card, you can display all the information reported by the BMS, exactly how to realize it? Below are a few cases about the actual use of our customers, to listen to what our customers say.
Real-time monitoring, supervision and protection of the battery unit.
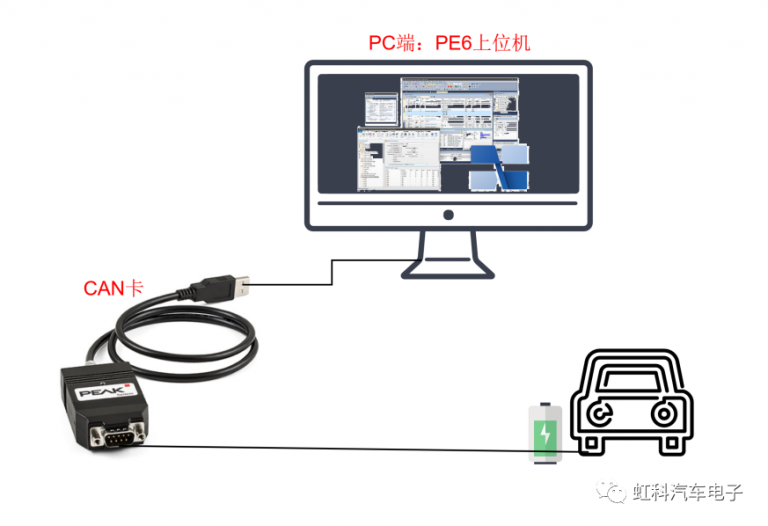
As shown in the figure above, PCAN is used to collect data from each battery, including temperature, voltage and other parameters, which is processed by the BMS to monitor the status of the battery cells in real time.The BMS continuously monitors the temperature, voltage and current of the battery packs using CAN communication and parses them on the host computer PE6 to detect any anomalies, such as overheating, overcharging, or over discharging, etc. The BMS is also able to monitor the battery packs' temperature, voltage and current continuously using the BMS's CAN communication and parses them on the host computer PE6 to detect any anomalies, such as overheating, overcharging or over discharging, etc.
III. Battery Group Balancing
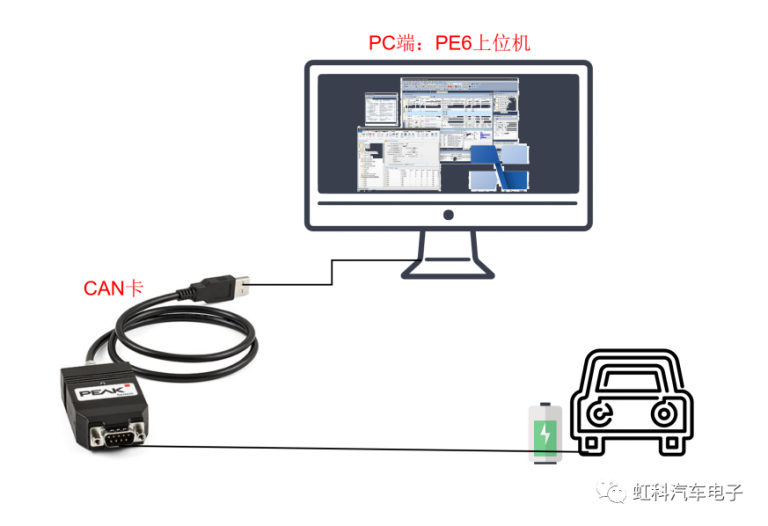
As shown in the figure above, the test environment is to simulate the whole vehicle, test the on-board power supply, the protocols used are the standard CAN FD and CAN2.0, PCAN-Explorer 6 can connect to several CAN and CAN FD networks at the same time, this test is required in accordance with the customer's DBC file and the product communication, data interaction, and can be graphically represented by the field record or the sequence of signals based on the trace. This test requires communication with the product according to the customer's DBC file for data interaction and can be graphically represented as a field record or as a trace-based signal sequence.
Conclusion
In conclusion, CAN communication technology has become an important component of the BMS for electric vehicles; PCAN is currently used in the BMS system to detect battery pack parameters, such as voltage, current, temperature, etc., in addition to controlling a variety of functions of the vehicle. Its application in real-time monitoring, fault detection and isolation, battery pack balancing, and safety monitoring and protection makes electric vehicles safer, more reliable and more efficient. Continued use of PCAN in the BMS to communicate will make electric vehicles more convenient and intelligent.