- Home
- Technical Products
Enterprise Cloud IT Solutions
Test Measurement
Industrial Measurement
- Solutions
Enterprise Cloud IT Solutions
Test Measurement
- Resource Center
- About Us
EN
Ensenso 3D Stereo Camera XR Series
Direct access to data - modularized, with local data processing capabilities
- Combines modular design with an embedded system for flexibility and powerful local data processing
- Native data transfer for direct transfer of processing results instead of raw data for multiphase systems and other compute-intensive applications
- Flexible and adjustable, and with the GigE uEye camera, according to your needs to build a 3D camera system, can extend the working distance of up to 5 meters.
Ensenso XR Series 3D Vision Camera
The Ensenso XR series cameras combine modular design with embedded systems, a powerful projection unit with an integrated system-level chip that provides flexibility and powerful local data processing over distances of up to 5 m. The cameras also feature local data transfer, which reduces the load on the network by transmitting the results of the processing directly instead of the raw data. Supporting wireless transmission and flexible connectivity, the cameras are suitable for multiphase systems and other computationally intensive applications.
- For use in harsh environments: IP65/67 rated protection against dirt, dust, and splashing water.
- For use in difficult lighting conditions: 100W LEDs for easy capture of object images.
- Flexibility to adapt to work requirements: variable baseline, adjustable viewing angle, a variety of lens options
- Working distance up to 5m: Larger working distance extension.
- Integrated Gigabit Ethernet: Customized 3D Camera System with Eye CP Camera
- Capture objects up to 8m³ in volume: Adjustable camera mounting extension working distance.
- FlexView2 Multi-Image Acquisition Technology: Delivering Higher Accuracy
- Data Processing in FPGA: Built-in Chip Realizes Native Data Processing Functions
- GigE interface and wireless transmission: flexible connectivity, temporary access to data parameters
- Ensenso SDK is easy to set up and operate: GPU-based image processing is also included!
Robotics Automation
Robots utilize data captured by 3D cameras for precise part grabbing, assembly and welding.
Quality Inspection and Testing
3D cameras are used to check the quality, size, integrity or location of products, such as automotive parts detection, workpiece surface defect detection, parts modeling, etc.
Logistics and Warehouse Automation
3D camera for automated parcel sorting or cargo stacking, such as feeding, palletizing/unloading, warehouse picking
Medical and Biomedical Imaging
3D cameras are used for body scanning, surgical assistance, or for imaging in other medical applications.
Product Advantages
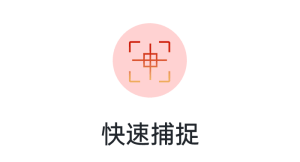
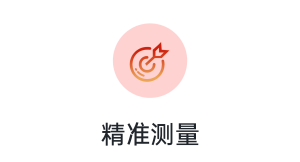
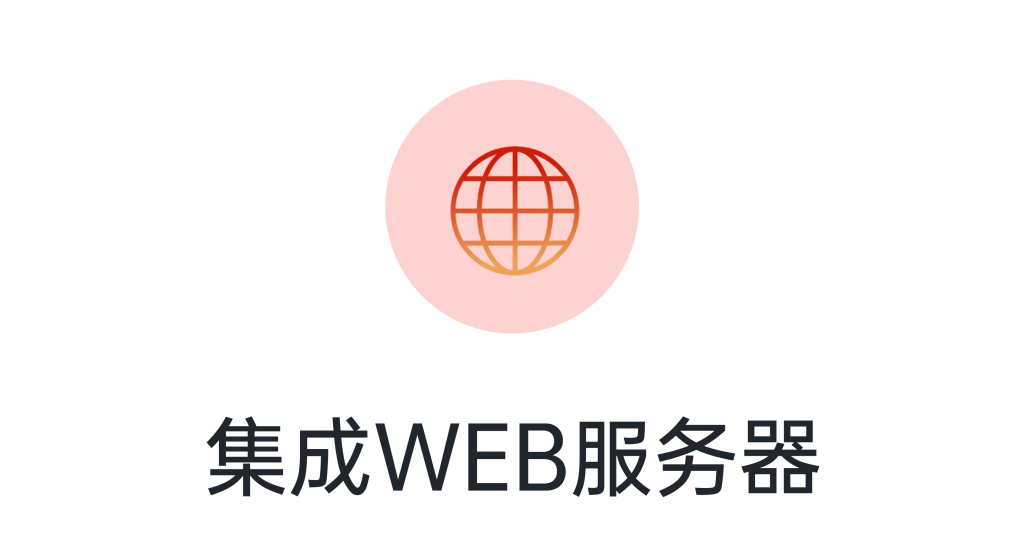
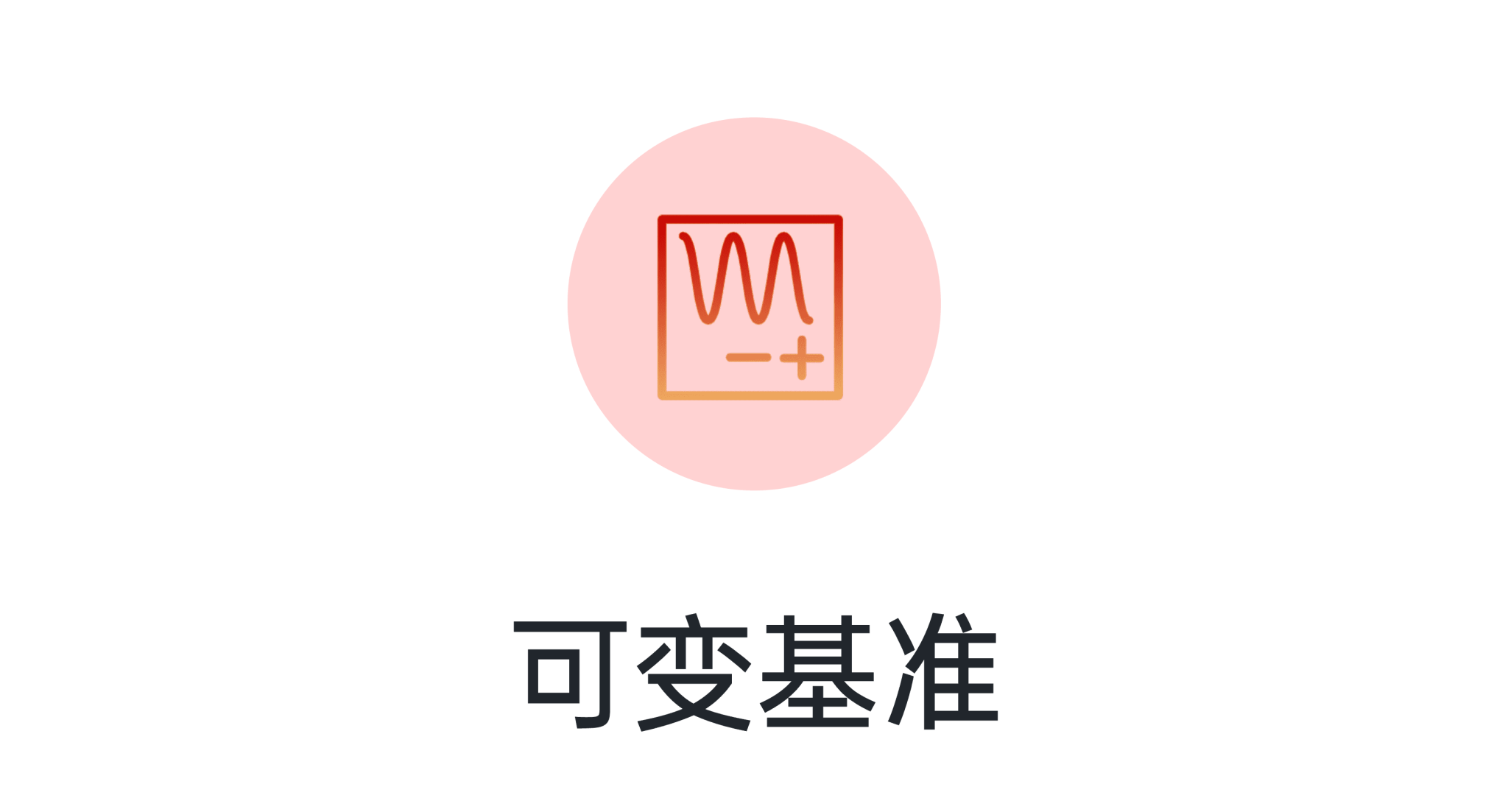
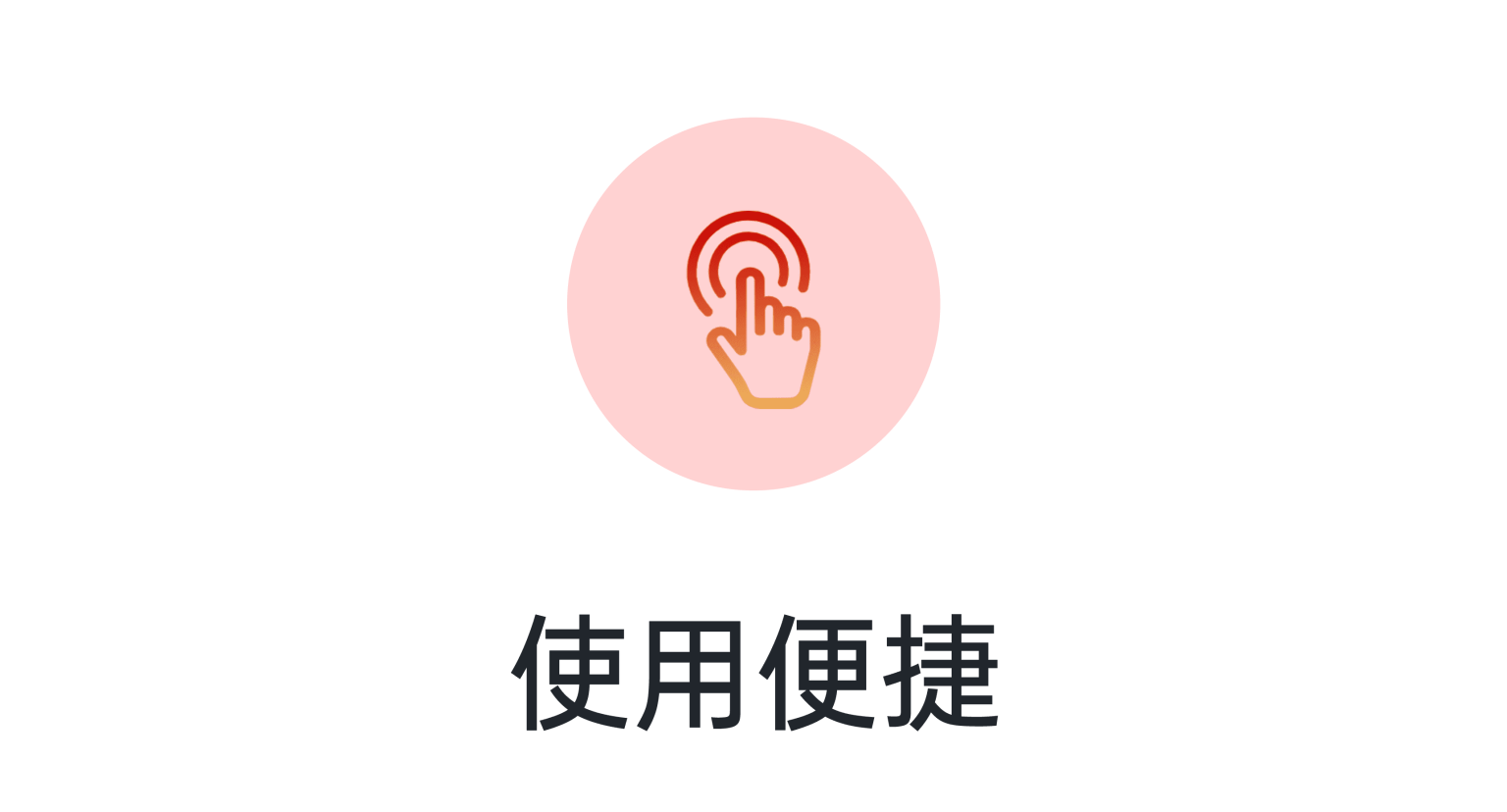
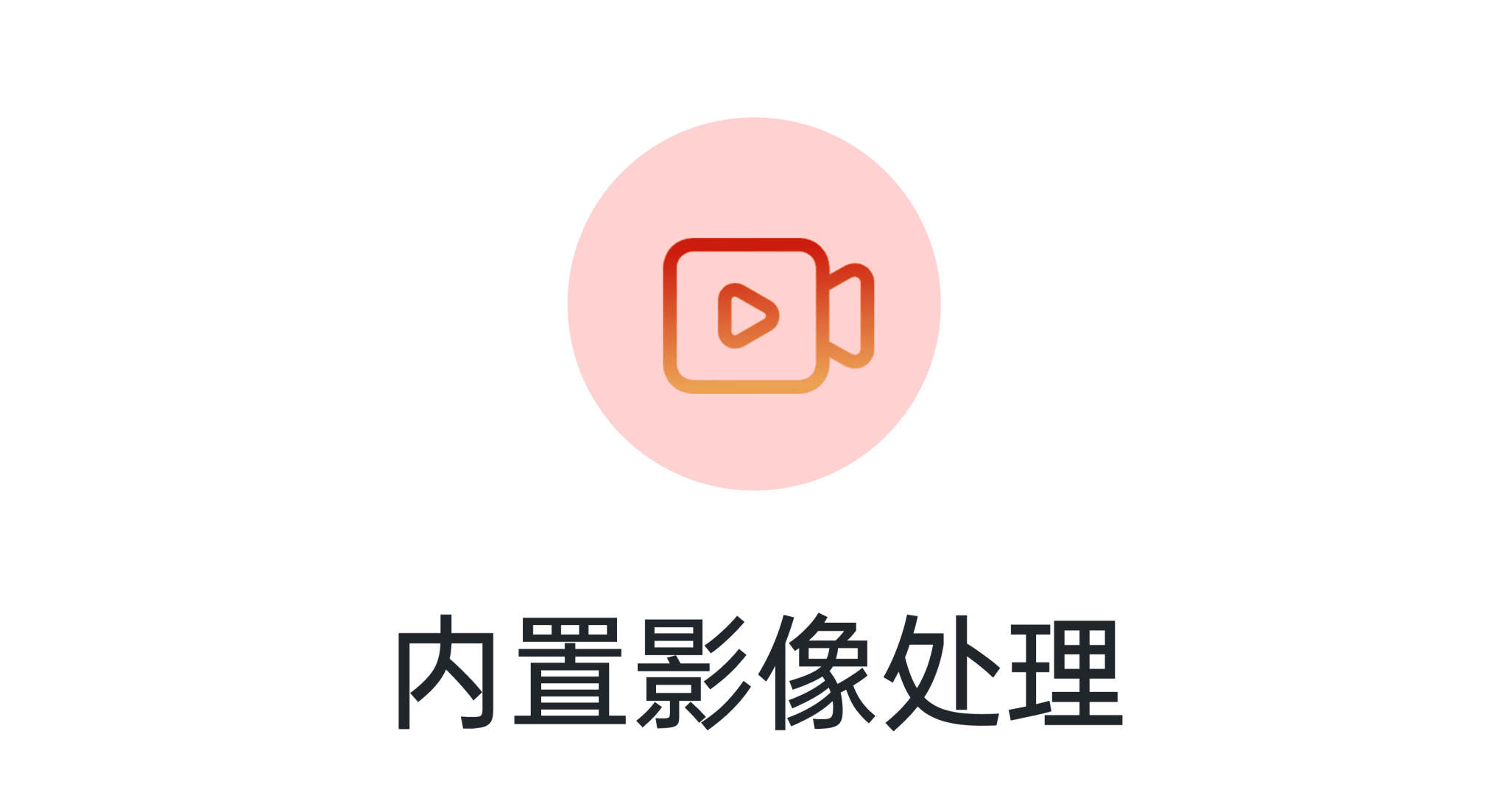
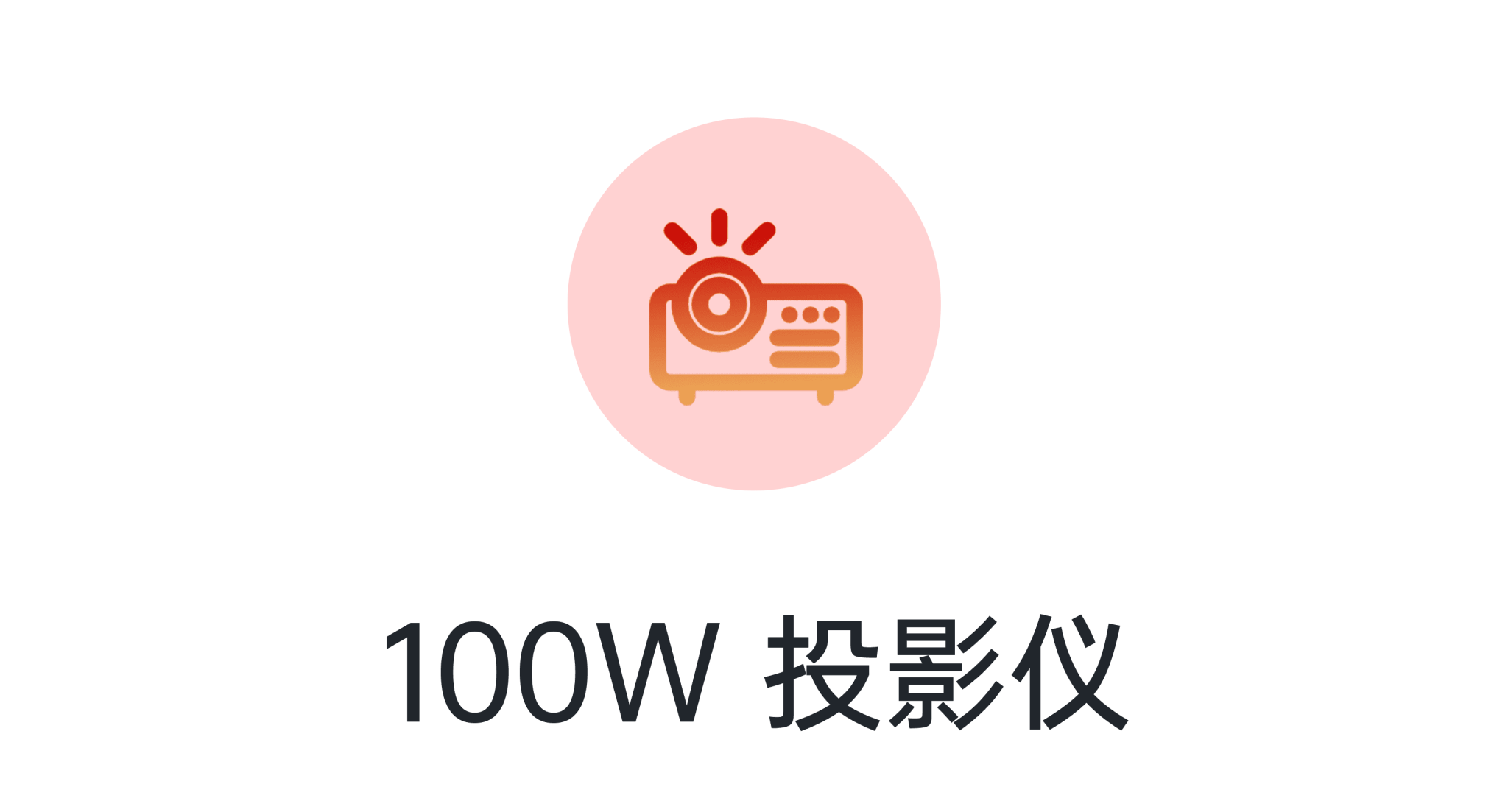
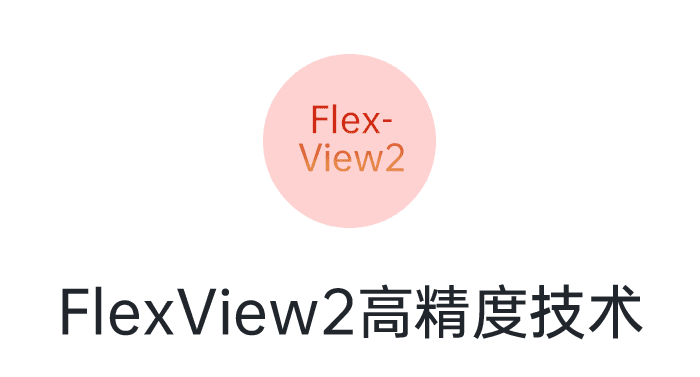
Modular design and embedded system integration
The Ensenso XR series cameras have the advantage of a flexible modular design and embedded system. The powerful projection unit with integrated system level chip can process image data independently and the camera outputs 3D data directly.
The 3D performance of the XR camera series rivals that of the powerful Core i7 processor. Complex data calculations can be done on the camera, eliminating the need for industrial calculators to process the data.
GigE data interface + wireless transmission function
The built-in headlamp supports calibration of the working environment and 2D image quality. In addition to the GigE data interface, the Ensenso XR series also supports wireless transmission.
Wireless transmission is very useful for temporary access to data and parameters when routing is difficult or costly.
Flexibility to adjust to the individual needs of the project
The XR series cameras can be flexibly adjusted and paired with the GigE uEye cameras to create a 3D camera system according to your needs, similar to the X camera series.
By selecting different baselines and focal lengths, the working distance can be extended to as far as 5 meters, and images of objects up to several cubic meters in size, such as heavy-duty pallets, or even entire rooms, can be captured.
Flexibility of adjustment facilitates a variety of settings at working distances of more than five meters, allowing the user to capture object volumes of more than three cubic meters, such as large, heavy pallets or entire rooms.
You can choose to use a 1.6-megapixel resolution camera or a 5-megapixel resolution camera for applications that require a larger field of view and more detail.
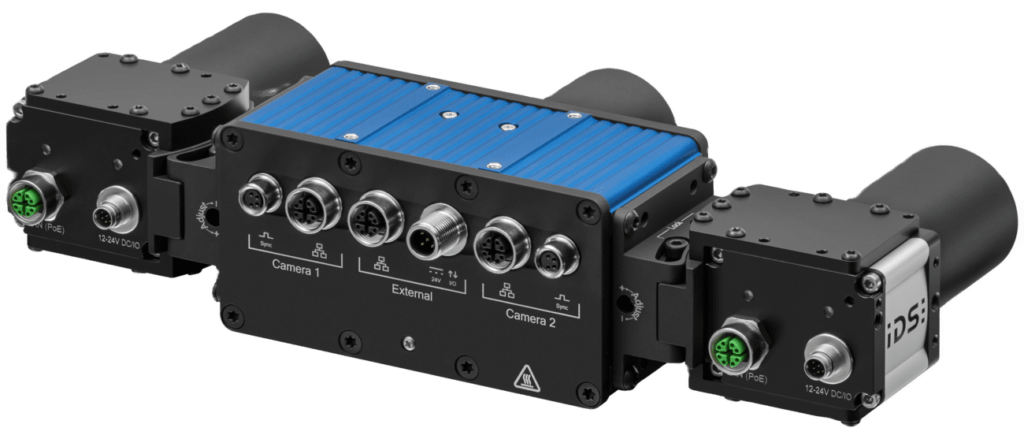
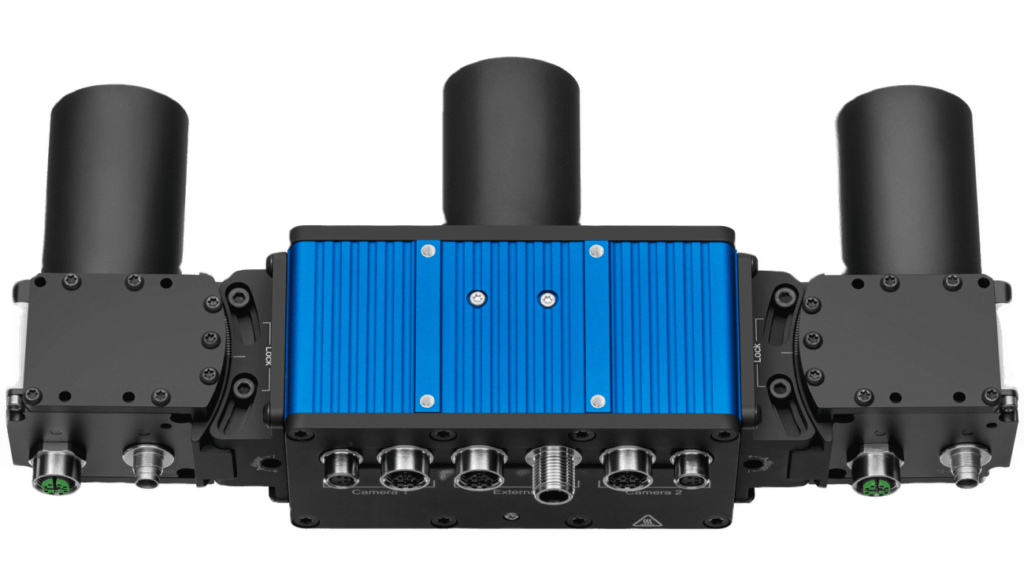
Ensenso SDK is provided for easy operation of the product.
With the Ensenso SDK, the Ensenso N Camera Series cameras are easy to set up and operate.
In addition to providing easy-to-configure wizards and camera calibration support for 3D cameras, it also includes GPU-based image processing for faster 3D data processing.
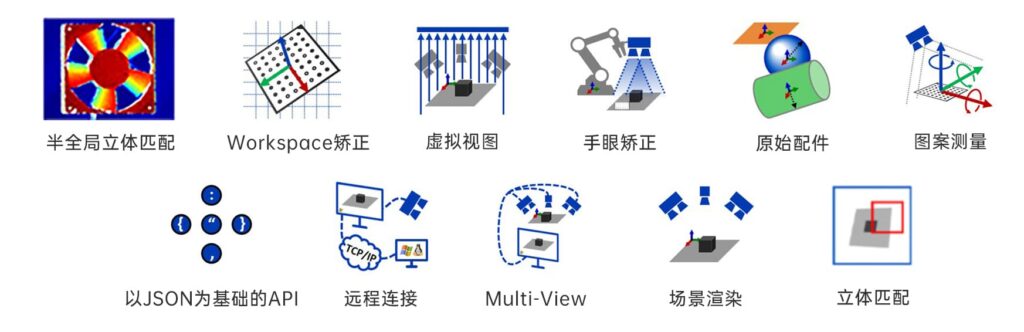
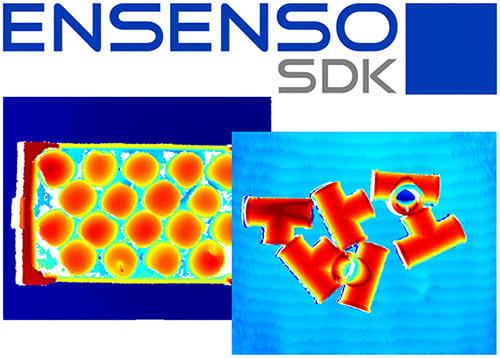
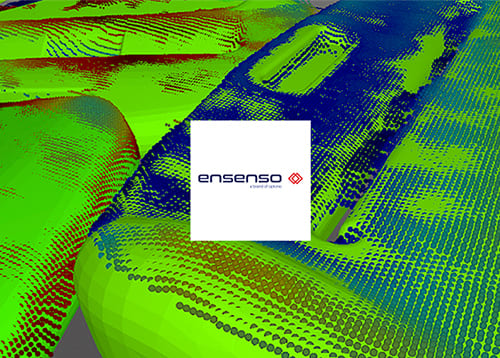
Technical Articles
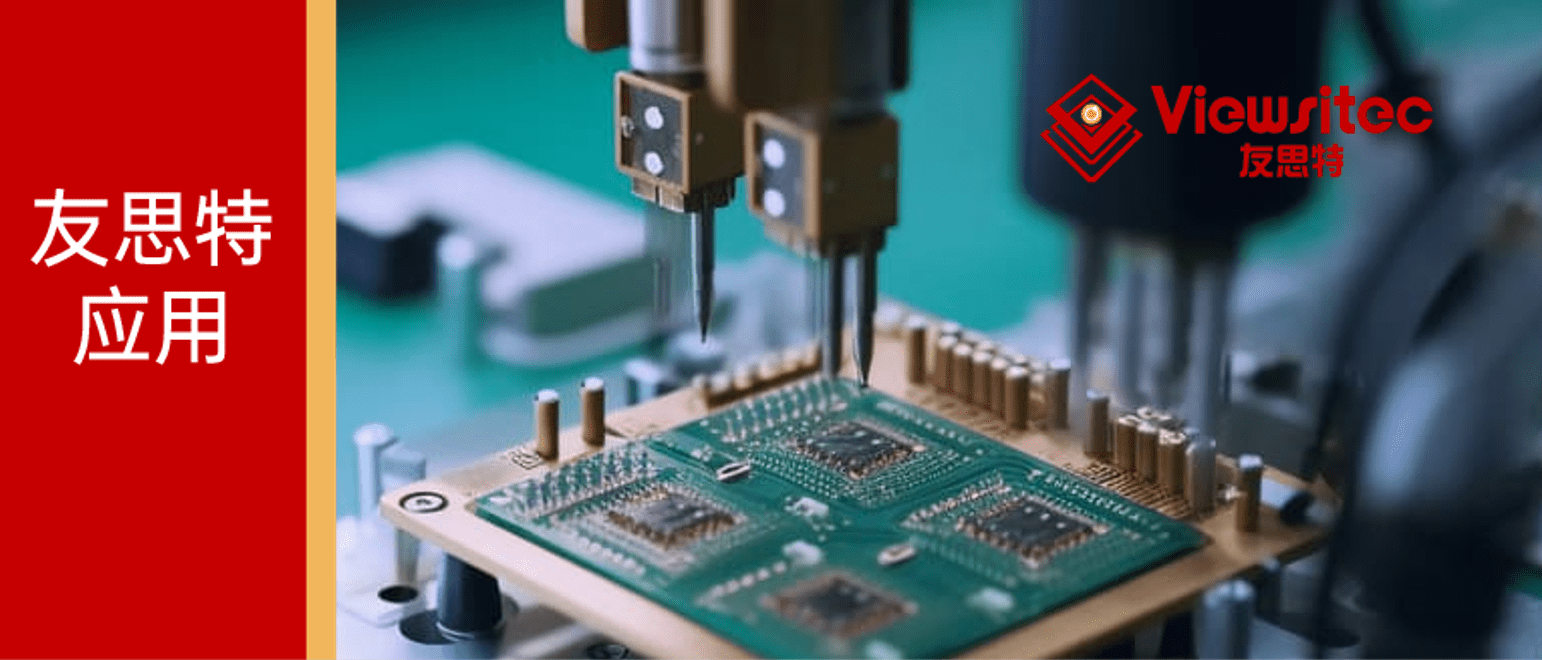
Terasic Solutions| Visual Inspection of PCB Assembly Screws Based on 3D Point Cloud
3D point cloud is the latest vision technology to accomplish precision PCB detection. Youstar's Saccde Vision visual scanning system utilizes advanced 3D imaging technology and algorithms to output intuitive point cloud images, further ensuring the reliability and stability of PCB production.

Terasic Solutions| PartFinder Module-based Algorithm for Workpiece Point Cloud Detection and Positioning Applications
Based on the Part Finder module and Ensenso3D camera equipment, the workpiece point cloud inspection and positioning application solution launched by Terasic is able to realize part identification and segmentation, and cooperate with the control of robot arms and other equipment movements to significantly improve the efficiency and accuracy of automated loading/unloading and segregation systems.
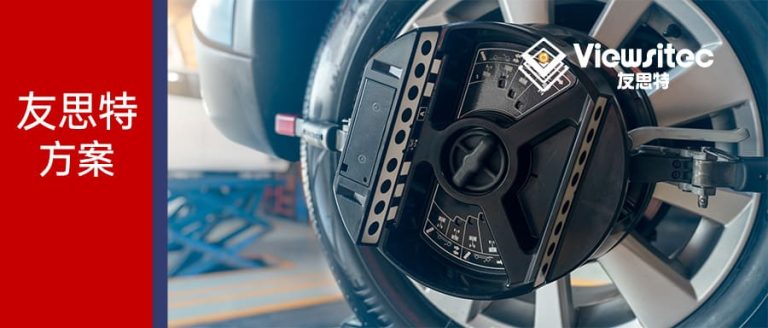
Terasic Solutions| FPGA-based 3D Camera for Tire Positioning and Inspection Applications
Based on Youstar Ensenso series of high-precision 3D camera real-time acquisition of the four wheels of the vehicle three-dimensional point cloud, capture key information and computing analysis to achieve accurate measurement of vehicle four-wheel alignment, the vehicle tire angle, tilt, front and rear wheel alignment, angle and other data to monitor and analyze the real-time, so as to timely detection and correction of tire problems, are widely used in automobile factories, the first assembly plants, repair stations and other venues. It is widely used in automobile factories, first assembly plants, repair stations and other places.
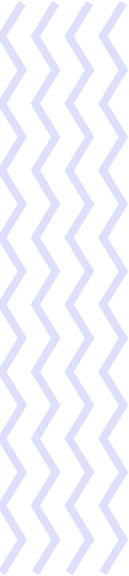
More Products
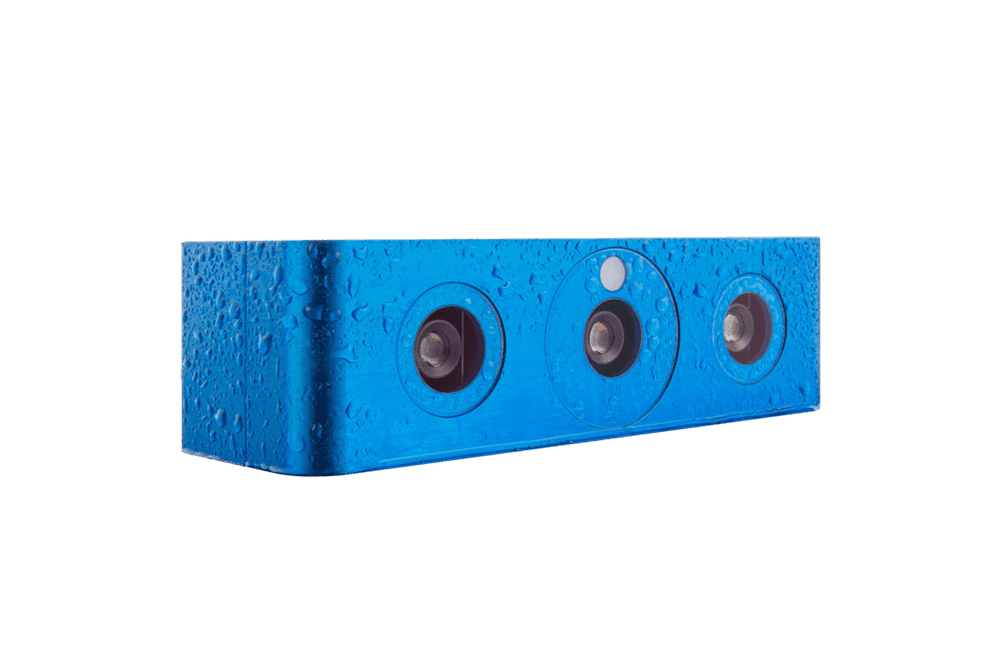
N Series 3D Stereo Camera
Precise, robust, easy to use
Compact and rugged 3D camera system designed for use in harsh environmental conditions
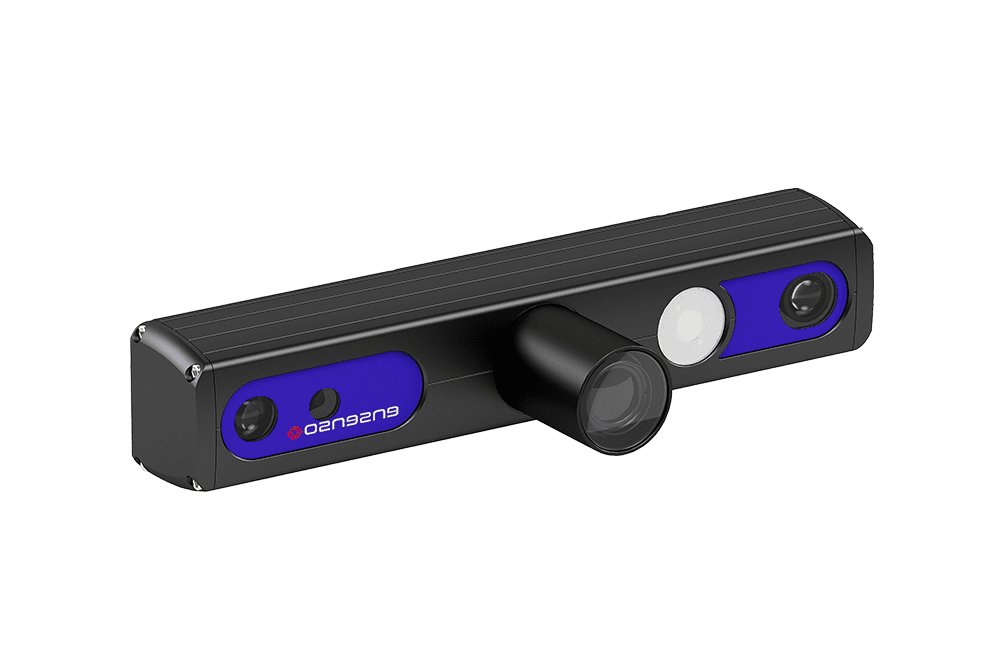
C-Series Color RGB 3D Stereo Camera
Equipped with fully integrated RGB sensor
Various models are available with a choice of baseline length (S:240 mm, M:455 mm) and focal length.
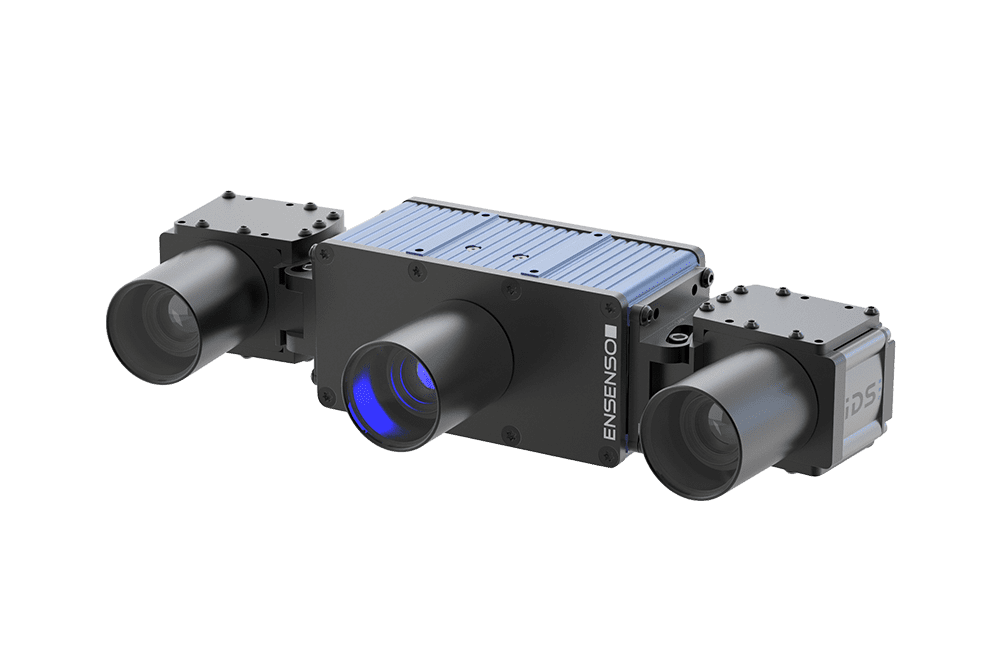
X-Series Modular 3D Stereo Camera
Modularity allows for flexibility and adaptability to project needs.
External lens, variable baseline, adjustable viewing angle, selectable lenses, 160w/500w high-resolution options available
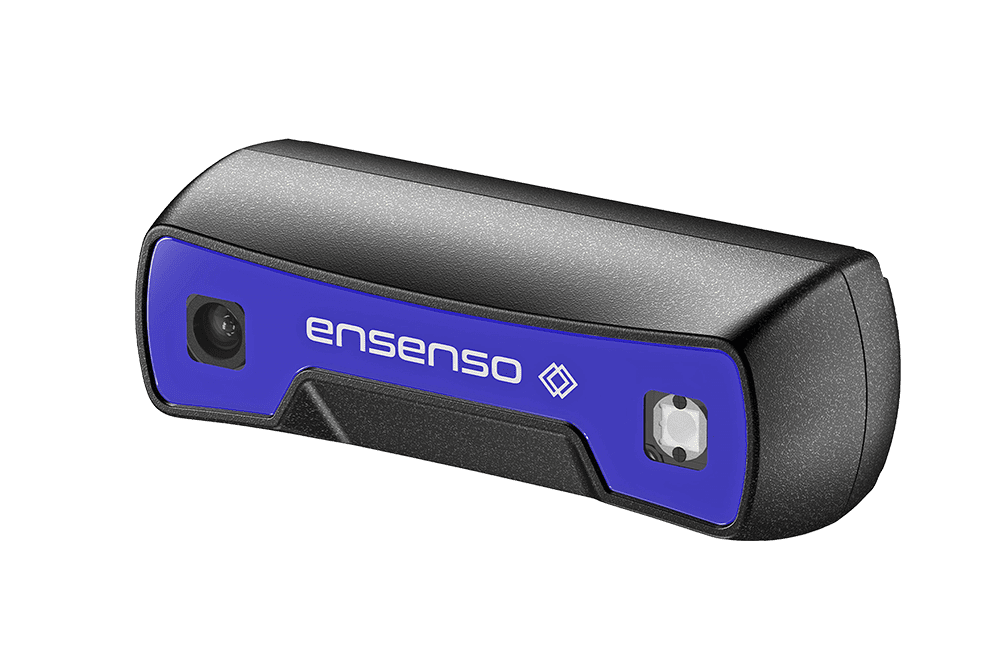
S-Series 3D Stereo Camera
Ultra compact, high precision depth, TOF principle
Utilizes AI's 3D laser dot-matrix pattern triangulation technology for multiple scenes and ultra-compact designs.
Professional technical support from HONGKEI to help you succeed in your project.
As a provider specializing in machine vision and optoelectronic inspection solutions, Avision is also committed to providing you with a range of paid technical services related to this product, aiming to help you succeed in your project in the most cost-effective way. Please contact us if you need technical services related to this product!
Frequently Asked Questions
Technical support and paid services to drive your project to the limit.
What are the features of the different 3D cameras in the S-Series, N-Series, X-Series and XR-Series?
S series camera with the other three series of different technical principles applied, S series application is TOF laser triangulation principle, mainly rely on the laser transmitter and receiver to collect distance information, fixed field of view, high frame rate, low price. The other three series are applied to the principle of binocular scattering, high precision, of which the X series compared to the N series, the lens external, you can easily adjust the angle of the two cameras to adjust the field of view, and stronger anti-sunlight performance. The XR series supports data processing on the camera side, which can release the computing pressure on the processor side of the industrial control machine and improve efficiency.
FlexView is our core patented technology. The principle of FlexView is to capture 8 or 16 pairs of images from the left and right cameras at the same time, and then integrate the results of the multiple pairs of images into a single image, resulting in a depth image with higher precision, reliability, and finer details.
We apply the principle of binocular plus projector projection random scattering texture, in the traditional binocular parallax calculation measurement principle, an additional projector active projection texture to the target object, when the target object is not enough features, the images collected by the two cameras can be accurately parallax calculation, and then get the depth image and 3D point cloud.
1. What is the content of the test? Does the size/shape vary? What is the size range? Can you provide pictures/video?
2. Is the test in motion or static? Outdoor or indoor? Can you provide a movie of the working environment?
3. How long does the camera work?
4. Precision requirements?
5. Need RGB information?
6. Is the visual processing software being developed in-house or by a third party?
There are 3 holes for PoE, one round hole for the power adapter, and two network cable connectors, the one labeled OUT connects to the camera's network port, and the one labeled IN connects to the control terminal (e.g., computer).
- Our 3D cameras use the binocular scattering principle, which is capable of handling even difficult lighting conditions. And with our patented FlecView technology, both moving and stationary objects can be detected with an accuracy of up to about 0.1mm.
- We are modular, lightweight design, small and flexible, because the size will affect the robot/system design and carrier design, which is especially important for the collaborative robot, the camera is too heavy will occupy the payload of the arm.
- We provide C, C++, C#, Halcon, and ros interface APIs, which are convenient for users to develop and use. And our SDK is very stable and easy to use, which is very important for the long-term use of enterprises and product reputation. This is also the reason why many leading companies, such as Mitsubishi, Damien, Makin, Amazon, etc., choose us.
- The protection level is IP65/67, supporting a wide range of indoor and outdoor scenarios, and adapting to harsh environments such as industrial applications.
Open PC Control Panel->Network and Sharing Center->Change Adapter Settings->Select the right-click attribute of the Ethernet you just connected->Select IPv4->Assign IP address.
1. What is the content of the test? Does the size/shape vary? What is the size range? Can you provide pictures/video?
2. Is the test in motion or static? Outdoor or indoor? Can you provide a movie of the working environment?
3. How long does the camera work?
4. Precision requirements?
5. Need RGB information?
6. Is the visual processing software being developed in-house or by a third party?